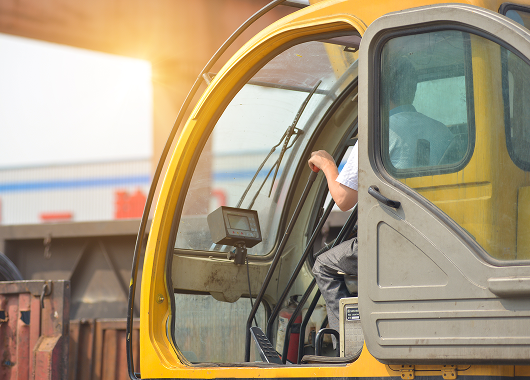
Maintenance Best Practices for Lifting Equipment
Share
Maintenance is the cornerstone of safe, efficient lifting operations. Without a robust maintenance routine, even the most advanced hoisting equipment is prone to unexpected downtime, increased repair costs, and, most critically, safety hazards.
In this guide, we explore best practices that ensure your lifting equipment remains reliable and performs at its best. From routine inspections and preventive care to leveraging modern monitoring technologies and adhering to strict safety standards, proper maintenance not only extends the lifespan of your machinery but also protects your workforce and investment.
Whether you’re managing industrial cranes, hoists, or any other lifting devices, establishing a systematic maintenance strategy is key to operational excellence and safety.
1. Establish a Routine Inspection Schedule
-
Daily Visual Checks: Before each use, inspect cables, hooks, chains, and other lifting components for signs of wear, deformation, or damage.
-
Pre-Shift Inspections: Ensure all safety devices, limit switches, and warning signals are functioning properly.
-
Post-Use Reviews: Document any unusual sounds, vibrations, or performance issues immediately after operations.
2. Implement a Preventive Maintenance Program
-
Manufacturer Guidelines: Follow the recommended maintenance schedule in the equipment manual, including lubrication, cleaning, and parts replacement.
-
Scheduled Overhauls: Set regular intervals for detailed inspections by certified technicians to prevent unexpected failures.
-
Calibration and Testing: Regularly calibrate load cells and conduct load tests to ensure the equipment is operating within safe parameters.
3. Focus on Cleaning and Lubrication
-
Routine Cleaning: Remove dirt, grease, and debris from critical components such as hooks, chains, and winches to prevent corrosion and deterioration.
-
Lubrication: Apply appropriate lubricants to moving parts as specified by the manufacturer to reduce friction and wear.
-
Corrosion Prevention: For equipment used in harsh environments, use anti-corrosion coatings and store the equipment in controlled conditions when not in use.
4. Maintain Accurate Records and Documentation
-
Maintenance Logs: Keep detailed records of all inspections, maintenance work, and repairs. This documentation is essential for tracking equipment performance over time.
-
Compliance Reports: Ensure that maintenance records comply with local regulations and industry standards, such as those from OSHA or ISO.
-
Incident Reporting: Document any incidents or near-misses and follow up with corrective actions to prevent future occurrences.
5. Train and Certify Operators
-
Regular Training: Ensure that operators are trained not only in equipment operation but also in basic maintenance and daily inspection procedures.
-
Certification Programs: Encourage or require operators to undergo certification programs that include safety and maintenance best practices.
-
Feedback Loop: Establish a system for operators to report issues or suggest improvements in maintenance practices.
6. Embrace Technological Advancements
-
Remote Monitoring: Use sensor technologies and IoT solutions to continuously monitor equipment health and predict maintenance needs before issues escalate.
-
Software Solutions: Implement computerized maintenance management systems (CMMS) to streamline scheduling, tracking, and reporting of maintenance activities.
-
Upgrade Legacy Equipment: Where possible, retrofit older equipment with modern safety and monitoring features to extend its lifespan and improve safety.
7. Adhere to Safety and Regulatory Standards
-
Follow Regulations: Always comply with national and local safety regulations, such as OSHA guidelines, to ensure a safe work environment.
-
Periodic Audits: Conduct regular safety audits and inspections to verify that maintenance practices meet required standards.
-
Emergency Preparedness: Develop and rehearse emergency procedures in case of equipment failure, ensuring that all personnel know how to respond safely.
Conclusion
By establishing a rigorous maintenance routine, adhering to manufacturer guidelines, investing in training, and leveraging technology, companies can significantly reduce downtime, prevent accidents, and extend the life of their lifting equipment. Maintaining equipment isn’t just about compliance—it’s a key element in ensuring a safe, efficient, and productive work environment.